Oct 11, 2023
How to Improve Warehouse Efficiency and Reduce Costs.
Optimizing warehouse operations is a strategic imperative factor to your eCommerce store’s efficiency and cost reduction. An efficient warehouse directly correlates to a streamlined process, lowering costs and enhancing customer satisfaction. This article will take an in-depth look at a range of actionable strategies and practices that can leverage your company to gain a competitive edge.
Understanding warehouse efficiency
Efficient warehouse operations play a crucial role in ensuring smooth supply chain management and customer satisfaction. A well-functioning warehouse can increase operational productivity, reduce lead times, minimize errors, and optimize resource utilization.
When it comes to warehouse efficiency, there are several factors that come into play. One of the key aspects is the layout and organization of the warehouse itself. A well-designed layout can minimize the time and effort required to move goods from one location to another, reducing the chances of bottlenecks and congestion.
Another important factor is the use of technology and automation. Modern warehouses are increasingly adopting technologies such as barcode scanning, RFID tagging, and automated material handling systems. These technologies not only improve accuracy and speed but also enable real-time tracking and monitoring of inventory.
The importance of warehouse efficiency
Warehouse efficiency is paramount for several reasons. Firstly, efficient operations enable quicker turnaround times for order processing, allowing companies to meet customer demands promptly. This is especially important in today’s fast-paced e-commerce environment, where customers expect their orders to be fulfilled rapidly.
Secondly, streamlined warehouse processes lead to higher accuracy levels, reducing the likelihood of shipment errors and the associated costs. By minimizing errors, companies can avoid the need for costly returns, replacements, and customer dissatisfaction.
Furthermore, efficient warehouse operations contribute to overall cost savings. By optimizing resource utilization and minimizing wastage, companies can reduce their operational expenses. This, in turn, can lead to improved profitability and a competitive advantage in the market.
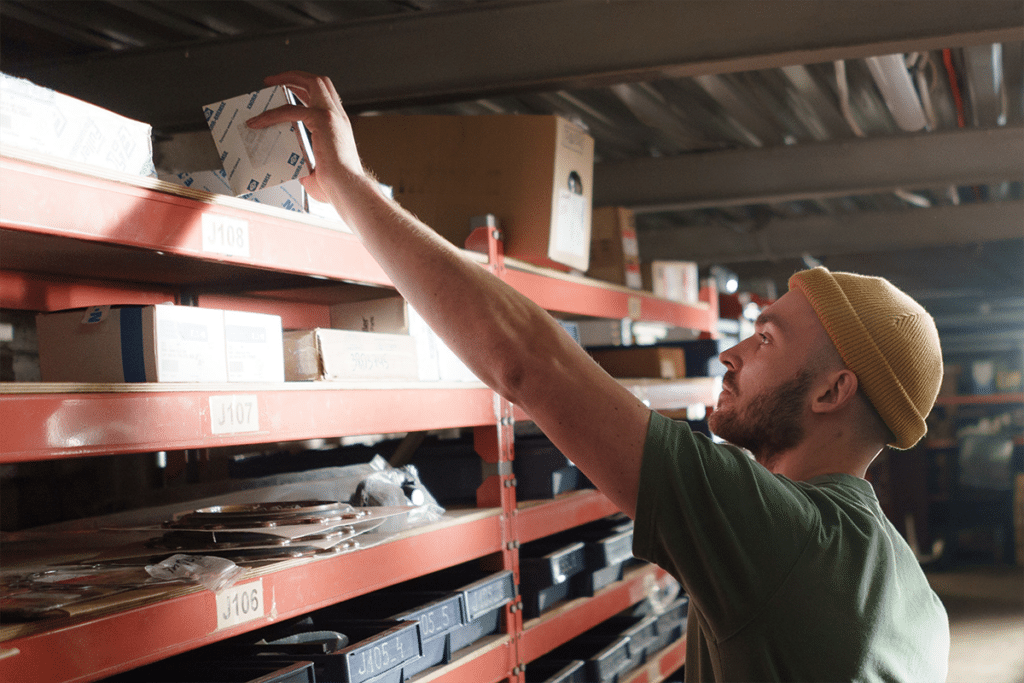
Key indicators of warehouse efficiency
To measure and monitor warehouse efficiency, companies need to consider key performance indicators (KPIs). These KPIs provide insights into the effectiveness of warehouse operations and help identify areas for improvement.
One important KPI is order picking accuracy. This metric measures the percentage of orders that are picked accurately without any errors. A high order picking accuracy indicates that the warehouse staff is performing their tasks diligently and that the inventory management system is reliable.
Another crucial indicator is the inventory turnover rate. This metric calculates how quickly inventory is being sold and replenished. A high turnover rate suggests that the warehouse is efficiently managing its inventory levels, avoiding overstocking or stockouts.
In addition to these KPIs, on-time delivery and labor utilization are also important indicators of warehouse efficiency. On-time delivery measures the percentage of orders that are delivered to customers within the promised timeframe. This metric reflects the warehouse’s ability to fulfill orders promptly and meet customer expectations.
Labor utilization, on the other hand, assesses how effectively the warehouse workforce is being utilized. It considers factors such as labor productivity, overtime hours, and absenteeism. By optimizing labor utilization, companies can ensure that their workforce is efficiently deployed and that tasks are completed in a timely manner.
By regularly tracking these indicators and analyzing the data, businesses can identify areas for improvement and implement targeted strategies. Continuous monitoring and improvement efforts are essential to maintaining and enhancing warehouse efficiency in an ever-evolving business landscape.
Strategies to improve warehouse efficiency
Implementing effective strategies is essential to optimize warehouse efficiency. Here are three key approaches:
Implementing lean principles
Adopting Lean principles and methodologies can significantly improve warehouse efficiency. Lean focuses on eliminating waste, optimizing workflows, and enhancing overall productivity. By implementing Lean practices such as 5S organization, standard work procedures, and visual management, companies can eliminate bottlenecks and streamline operations.
5S organization, one of the core principles of Lean, involves organizing the workspace to improve efficiency and productivity. This includes sorting, setting in order, shining, standardizing, and sustaining. By implementing this method, companies can reduce clutter, improve visibility, and create a more organized and efficient warehouse environment.
Standard work procedures help establish consistency and eliminate variations in processes. By defining and documenting standard operating procedures, companies can ensure that tasks are performed in the most efficient and effective way, reducing errors and improving overall productivity.
Visual management is another important aspect of Lean principles. By using visual cues such as color-coded labels, floor markings, and signage, companies can improve communication, reduce errors, and enhance overall efficiency. Visual management helps employees quickly locate items, identify workflow patterns, and understand the status of operations at a glance.
Optimizing warehouse layout
The physical layout of a warehouse can impact efficiency. By analyzing current workflows and product flow patterns, companies can optimize their warehouse layout. This may involve rearranging storage locations, establishing dedicated zones for high-demand items, and implementing intelligent slotting strategies. Such layout optimizations ensure that products are easily accessible, reducing travel distances and minimizing handling time.
When optimizing warehouse layout, it is important to consider factors such as product demand, order frequency, and storage capacity. By strategically placing high-demand items closer to the shipping area, companies can reduce picking time and improve order fulfillment speed.
Additionally, implementing intelligent slotting strategies, such as ABC analysis or velocity-based slotting, can further enhance efficiency by placing frequently picked items in easily accessible locations.
Furthermore, the use of technology such as warehouse management systems (WMS) can aid in optimizing warehouse layout. WMS software can provide real-time data on inventory levels, order volumes, and product locations, enabling companies to make data-driven decisions when designing their warehouse layout.
Investing in warehouse automation
Automation technologies, such as automated picking systems, conveyor belts, and robotics, can significantly enhance warehouse efficiency. These technologies automate repetitive tasks, reducing human error and increasing throughput. By investing in warehouse automation, companies can accelerate order fulfillment, improve inventory accuracy, and reduce labor costs.
Automated picking systems, such as pick-to-light or pick-to-voice systems, can expedite the picking process by guiding warehouse workers to the exact location of items. This reduces picking errors and increases productivity. Conveyor belts can streamline the movement of goods within the warehouse, eliminating the need for manual transportation and reducing handling time.
Robotics is another area of warehouse automation that has gained significant traction in recent years. Autonomous mobile robots (AMRs) can navigate warehouse aisles and perform tasks such as picking, packing, and sorting. By leveraging robotics, companies can achieve higher picking accuracy, faster order fulfillment, and improved overall efficiency.
It is important to note that while warehouse automation can bring numerous benefits, careful planning and integration are required. Companies need to assess their specific needs, evaluate the costs and benefits, and ensure proper training and maintenance to maximize the effectiveness of automation technologies.
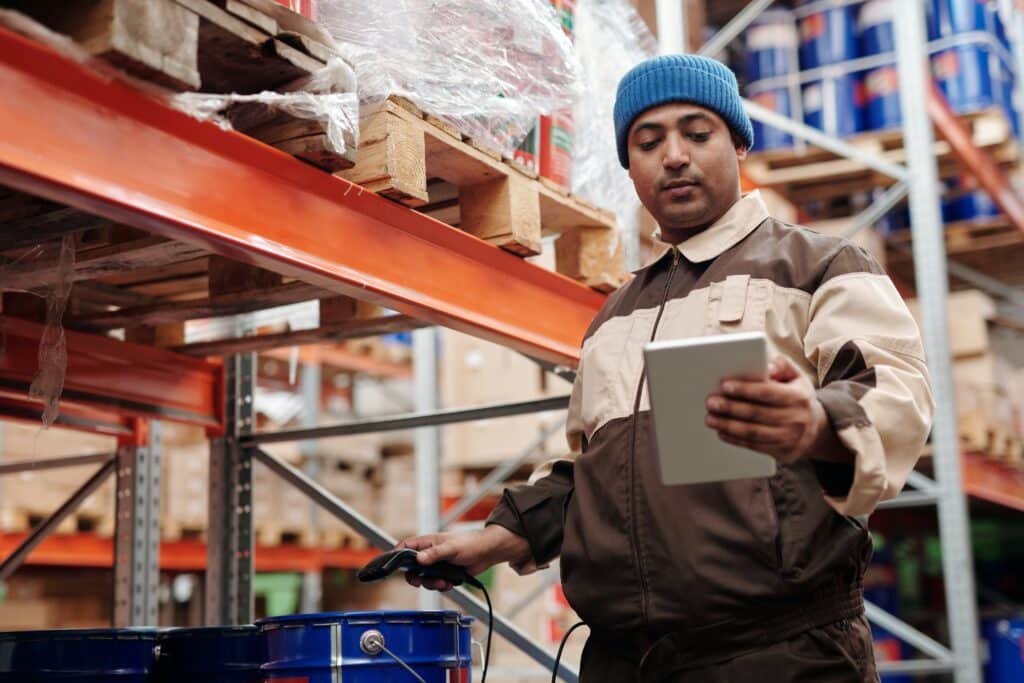
Reducing warehouse costs
In addition to improving efficiency, reducing warehouse costs is equally important for overall operational success. Here are three strategies to consider:
Streamlining inventory management
Effective inventory management is crucial for cost reduction. By implementing inventory control techniques such as ABC analysis and Just-in-Time (JIT) inventory systems, companies can optimize stock levels, reduce carrying costs, and prevent inventory obsolescence. Streamlining inventory management also enables faster order fulfillment and prevents stockouts.
Reducing energy consumption
Warehouse operations can be energy-intensive. By implementing energy-efficient lighting, HVAC systems, and equipment, companies can reduce energy consumption and significantly cut operating costs. Additionally, utilizing natural lighting, installing motion sensors, and properly insulating the warehouse can further contribute to energy savings.
Minimizing labor costs
Labor costs often constitute a significant portion of warehouse operating expenses. To minimize these costs, companies can employ several strategies. These may include cross-training employees, implementing incentive programs, optimizing workforce scheduling, and adopting performance-based pay structures. By enhancing employee productivity and reducing turnover rates, businesses can achieve substantial savings.
Monitoring and maintaining efficiency
Efficiency improvement efforts should not be limited to one-time initiatives. It is essential to continuously monitor and maintain efficiency levels in the warehouse. Here are two approaches:
Regular performance audits
Conducting regular performance audits helps identify areas for improvement and monitors progress. These audits involve analyzing various warehouse KPIs, evaluating process flows, and soliciting feedback from employees. Based on the findings, companies can implement corrective actions and fine-tune their strategies for ongoing efficiency gains.
Continuous improvement in the warehouse
Adopting a culture of continuous improvement is crucial for sustained warehouse efficiency. Encouraging employee involvement in idea generation and process optimization fosters a sense of ownership and promotes innovation. By regularly seeking input and empowering employees, companies can drive positive change and stay ahead of the competition.
The impact of improved efficiency on business performance
Improving warehouse efficiency has several positive implications for overall business performance. Here are three key benefits:
Enhancing customer satisfaction
A well-optimized warehouse enables faster order processing, accurate order fulfillment, and timely deliveries. By meeting customer expectations consistently, businesses can enhance customer satisfaction levels, build loyalty, and strengthen their brand reputation.
Boosting profit margins
Efficiency improvements in warehouse operations often lead to cost savings, resulting in increased profit margins. By reducing labor costs, inventory carrying costs, and energy expenses, companies can allocate resources more effectively and generate higher profits.
Strengthening competitive advantage
Efficient warehouse operations provide a competitive advantage in the marketplace. By delivering products quicker and with fewer errors than competitors, companies can differentiate themselves, attract more customers, and capture a larger market share.
In conclusion, improving warehouse efficiency and reducing costs are essential for businesses looking to thrive in today’s demanding market. By understanding the importance of warehouse efficiency, implementing effective strategies, and continuously monitoring performance, companies can achieve operational excellence, enhance customer satisfaction, and drive profitability.
Make post-purchase offers that increase AOV.
Start today,
for free
Start a free trial of any of AMP’s tools today.